Revolution in der Statorausrüstungsindustrie
In den letzten Jahren haben Branchen weltweit dank technologischer Durchbrüche, die unser Leben verändert haben, erhebliche Fortschritte erzielt. Ein Bereich, der davon maßgeblich betroffen ist, ist die Statorausrüstungsindustrie. Die Einführung modernster Technologien hat hier eine Revolution durchgemacht, die zu verbesserter Funktionalität, Effizienz und Leistung geführt hat.
Der Stator ist ein wesentlicher Bestandteil verschiedener Maschinen wie Elektromotoren und Generatoren. Er sorgt für die Rotation der festen Systemteile und erzeugt elektromagnetische Felder, die für die Funktion dieser Geräte entscheidend sind. Traditionell basiert die Statorkonstruktion auf konventionellen Konstruktionen, was ihre Leistung und Anpassungsfähigkeit einschränkt.
Doch mit dem Aufkommen technologischer DurchbrücheStatorausrüstungDie Branche hat einen Paradigmenwechsel erlebt. Einer der bedeutendsten Fortschritte ist die Entwicklung des 3D-Drucks in der Statorfertigung. Diese bahnbrechende Technologie ermöglicht komplexes Design und präzise Anpassung und ermöglicht so die Herstellung von Statorausrüstung, die spezifische Anforderungen perfekt erfüllt. Darüber hinaus reduziert der 3D-Druck Produktionszeit und -kosten erheblich und macht Statorausrüstung zugänglicher und erschwinglicher als je zuvor.
Ein weiterer wichtiger technologischer Durchbruch in der Statorausrüstungsindustrie ist die Implementierung intelligenter Sensoren, die in das IoT (Internet of Things) integriert sind. Durch die Integration von Sensoren in die StatorausrüstungHerstellerkann Echtzeitdaten zu Leistung, Temperatur und Vibration überwachen und erfassen. Diese Daten ermöglichen vorausschauende Wartung, frühzeitige Fehlererkennung und optimierte Betriebseffizienz. Diese Fähigkeiten werden durch die Integration von IoT-Technologie weiter verbessert, die eine Fernüberwachung und -steuerung von Statoranlagen unabhängig vom geografischen Standort ermöglicht.
Darüber hinaus tragen Fortschritte in der Materialwissenschaft zur Verbesserung der Leistung von Statoranlagen bei. Die Entwicklung neuer Materialien, wie beispielsweise Speziallegierungen und Verbundwerkstoffe, ermöglicht Statoranlagen eine höhere Festigkeit, Hitzebeständigkeit und elektrische Leitfähigkeit. Diese Fortschritte gewährleisten Langlebigkeit und Zuverlässigkeit und reduzieren Wartungskosten und Ausfallzeiten.
Insgesamt haben technologische Durchbrüche die Statorindustrie grundlegend verändert. Der Einsatz von 3D-Druck, die Integration intelligenter Sensoren und des Internets der Dinge sowie Fortschritte in der Materialwissenschaft heben Funktionalität und Effizienz von Statorgeräten auf ein neues Niveau. Diese Revolution ebnet den Weg für eine Zukunft, in der Statorgeräte eine entscheidende Rolle in der nachhaltigen Energieerzeugung, im Transportwesen und in industriellen Anwendungen spielen. Da sich die Technologie ständig weiterentwickelt, können wir uns auf weitere Innovationen und die Entdeckung neuer Möglichkeiten in diesem faszinierenden Bereich freuen.
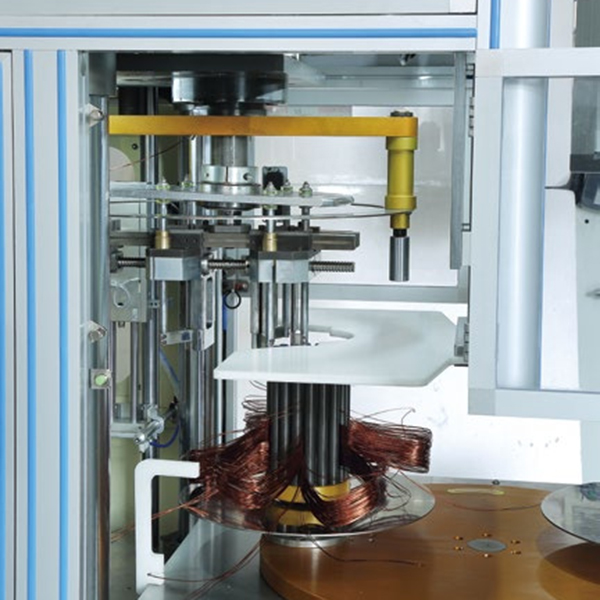
Häufige Herausforderungen bei der Herstellung von Statorausrüstung
Häufige Herausforderungen bei der Herstellung von Statoren ergeben sich aus traditionellen Methoden mit manuellen Produktionsprozessen. Diese Methoden sind nicht nur zeitaufwändig, sondern auch arbeitsintensiv und anfällig für menschliche Fehler. Ältere Fertigungstechnologien verschärfen diese Probleme zusätzlich, indem sie Design und Funktionalität der Statoren einschränken und so Leistung und Effizienz beeinträchtigen. Daher ist der Bedarf an innovativen und fortschrittlichen Fertigungstechnologien in der Statorindustrie enorm gestiegen.
Herkömmliche Statorherstellungsverfahren erfordern die manuelle Montage jedes Bauteils durch Facharbeiter. Diese manuelle Arbeit erhöht nicht nur die Produktionszeit, sondern birgt auch das Risiko menschlicher Fehler. Jeder Stator ist ein komplexes Gerät mit verschiedenen komplexen Komponenten, die sorgfältig ausgerichtet werden müssen. Schon kleinste Fehler können zu Ineffizienz und verminderter Produktqualität führen. Diese Herausforderungen werden durch die mangelnde Konsistenz der manuellen Arbeit noch verschärft, was die Aufrechterhaltung der Konsistenz der Produktionschargen erschwert.
Eine weitere große Herausforderung bei der konventionellen Statorherstellung sind die Einschränkungen älterer Fertigungstechnologien. Diese Technologien schränken oft Design und Funktionalität der Statorausrüstung ein, behindern Innovationen und verringern die Gesamtleistung. Mit der technologischen Weiterentwicklung steigt die Nachfrage nach effizienteren Statorausrüstungen stetig. Mit herkömmlichen Fertigungsmethoden wird die Integration neuer Designmerkmale und die Verbesserung der Leistung jedoch zu einem erheblichen Hindernis.
Um diesen Herausforderungen zu begegnen, setzen Hersteller zunehmend auf fortschrittliche Technologien wie automatisierte Produktionsprozesse und computergestütztes Design (CAD). Diese Innovationen revolutionierten die Herstellung von Statoranlagen, indem sie die Produktion rationalisierten, die Konsistenz verbesserten und die Gesamtproduktqualität steigerten.
Automatisierte Produktionsprozesse machen manuelle Arbeit überflüssig und ermöglichen eine schnellere und präzisere Fertigung. Moderne Maschinen und Roboter können komplexe Montageaufgaben präzise erledigen und so das Risiko menschlicher Fehler reduzieren. Dies verbessert nicht nur die Produktionseffizienz, sondern sichert auch die Konsistenz und Qualität des Endprodukts. Hersteller können nun Kundenanforderungen effizienter erfüllen und Lieferzeiten verkürzen.
Computergestütztes Design (CAD) spielt eine entscheidende Rolle bei der Überwindung der Einschränkungen älterer Fertigungstechnologien. Mit CAD können Hersteller Statorkonstruktionen flexibler erstellen und verfeinern. Dies optimiert Leistung und Effizienz des Stators und verbessert somit die Gesamtsystemleistung. CAD ermöglicht es Herstellern außerdem, das Verhalten des Stators unter verschiedenen Betriebsbedingungen zu simulieren und zu analysieren und so sicherzustellen, dass die Konstruktion den erforderlichen Spezifikationen entspricht.
Darüber hinaus haben Materialverbesserungen, wie der Einsatz von leichten und leistungsstarken Verbundwerkstoffen, Statoranlagen nicht nur effizienter, sondern auch langlebiger und widerstandsfähiger gegen Umwelteinflüsse gemacht. Diese Materialien bieten verbesserte elektrische Isolationseigenschaften, reduzieren Verluste und erhöhen die Gesamteffizienz des Systems.
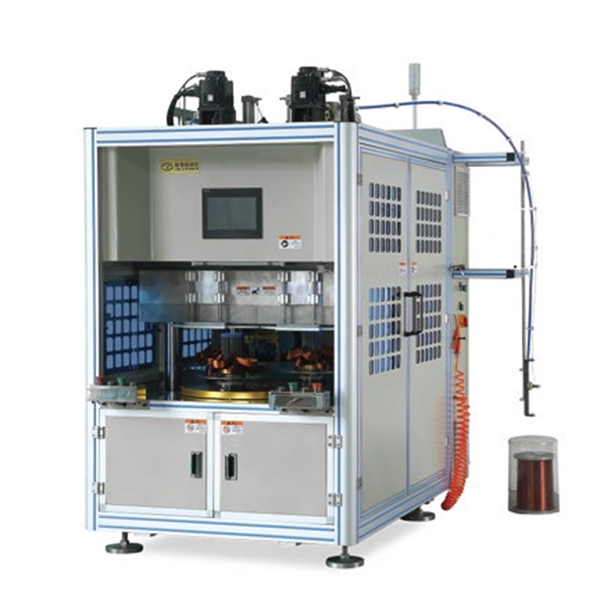
Fortschritte in der Fertigungstechnologie für Statorausrüstung
1.Automatisierung und Robotik in der Statorausrüstungsfertigung
Automatisierung und Robotik haben die Fertigung zweifellos revolutioniert, und die Herstellung von Statorausrüstung bildet da keine Ausnahme. Mit Fortschritten inAutomatisierung und RobotikModerne Fertigungsanlagen haben erhebliche Verbesserungen bei Produktivität, Effizienz und allgemeiner Produktqualität erzielt.
Ein Schlüsselbereich, in dem Automatisierung und Robotik die Herstellung von Statoranlagen maßgeblich beeinflussen, ist der Spulenwickelprozess. Der Einsatz von Roboterwickelmaschinen ersetzt manuelle Arbeit und ermöglicht präzise und konsistente Wickelmuster. Dies gewährleistet eine gleichmäßige Verteilung des elektromagnetischen Feldes im Stator. Dies verbessert nicht nur die Leistung der Statoranlage, sondern reduziert auch die Ausfallwahrscheinlichkeit und erhöht die Gesamtzuverlässigkeit der Anlage.
Ein weiterer Einsatzbereich von Automatisierung und Robotik in der Statorfertigung sind Prozesse wie Laminierung und Isolierung. Diese Aufgaben erfordern Präzision und Genauigkeit und können durch Automatisierung effizienter erledigt werden. Der Roboter kann die Statorkomponenten geschickt handhaben und die notwendigen Beschichtungen und Isolierungen fehlerfrei auftragen. Dies verbessert nicht nur die Qualitätskontrolle der Statorausrüstung, sondern reduziert auch die Abhängigkeit von Arbeitskräften und senkt somit die Arbeitskosten.
Der Einsatz von Automatisierung und Robotik in der Statorfertigung hat der gesamten Branche erhebliche Vorteile gebracht. Erstens steigert er die Gesamtproduktivität und die Produktionsgeschwindigkeit deutlich. Roboter können unermüdlich und ohne Pausen arbeiten, was einen effizienteren Fertigungsprozess ermöglicht. Zweitens kann die Automatisierung präzise und wiederkehrende Aufgaben konsistent ausführen, was hohe Genauigkeit gewährleistet und Fehler minimiert. Dies verbessert letztendlich die Produktqualität.
Darüber hinaus kann die Integration von Automatisierung und Robotik in die Statorfertigung zu Kosteneinsparungen führen. Die anfängliche Investition in Robotik- und Automatisierungssysteme kann zwar hoch sein, führt aber langfristig zu geringeren Arbeitskosten. Durch die Minimierung des manuellen Arbeitsaufwands und die Optimierung der Produktionseffizienz können Unternehmen erhebliche Kosteneinsparungen erzielen und ihre Wettbewerbsfähigkeit verbessern.
Laut einem Bericht von Marketsand Markets wird der globale Markt für Fertigungsroboter bis 2023 voraussichtlich ein Volumen von 61,3 Milliarden US-Dollar erreichen. Diese Prognose unterstreicht die wachsende Bedeutung und Nutzung von Automatisierung und Robotik in der Statorfertigung. Mit dem fortschreitenden technologischen Fortschritt sind auch in diesem Bereich weitere Fortschritte bei Automatisierung und Robotik zu erwarten.
AAutomatisierung und Robotik haben in der Statorfertigung erhebliche Fortschritte gebracht. Durch den Einsatz von Roboterwicklern und Automatisierung in Prozessen wie Laminierung und Isolierung können Hersteller Präzision verbessern, Geschwindigkeit erhöhen, Qualitätskontrolle optimieren und Arbeitskosten senken. Da die globale Fertigung zunehmend auf Automatisierung und Robotik setzt, müssen Statorhersteller diese Technologien nutzen, um wettbewerbsfähig zu bleiben und den wachsenden Marktanforderungen gerecht zu werden.
2. Fortschrittliche Materialien bei der Herstellung von Statorausrüstung
Moderne Werkstoffe haben die Herstellung von Statoranlagen revolutioniert und die Produktion dieser wichtigen elektrischen Komponenten revolutioniert. Die Integration von Materialien wie modernen Polymeren, Verbundwerkstoffen und Hochleistungslaminaten hat einen erheblichen Einfluss auf die Haltbarkeit, Wärmebeständigkeit und mechanische Festigkeit von Statoranlagen.
Einer der größten Vorteile des Einsatzes moderner Materialien bei der Herstellung von Statoren ist die Steigerung der Gesamteffizienz dieser Komponenten. Durch die Einführung leichter und hochpermeabler Materialien konnte die Leistung von Statoren deutlich verbessert werden. Diese Materialien ermöglichen nicht nur eine effizientere Energieübertragung, sondern tragen auch zur Reduzierung von Systemverlusten bei.
In den letzten Jahren haben Fortschritte in der Nanotechnologie die Entwicklung von Nanokompositmaterialien für Statorwicklungen weiter vorangetrieben. Diese Nanokomposite verfügen über eine hervorragende elektrische und thermische Leitfähigkeit, was zu einer höheren Leistungsdichte und geringeren Verlusten führt. Mit zunehmender Leistungsdichte werden Statoranlagen kompakter und effizienter, was zu Kosteneinsparungen für die Hersteller und einer verbesserten Systemleistung führt.
Die Integration moderner Materialien in die Statorfertigung ermöglicht es Herstellern zudem, langlebigere und zuverlässigere Produkte herzustellen. Beispielsweise bieten Hochleistungslaminate eine hervorragende Verschleißfestigkeit und stellen sicher, dass Statoranlagen den rauen Bedingungen standhalten, denen sie regelmäßig ausgesetzt sind.
Darüber hinaus tragen diese fortschrittlichen Materialien entscheidend zur Verbesserung der Sicherheit von Statoranlagen bei. Der Einsatz fortschrittlicher Polymere und Verbundwerkstoffe trägt dazu bei, die Isolationseigenschaften zu verbessern, Leckagen zu vermeiden und das Unfallrisiko zu verringern.
Unternehmen, die sich auf die Herstellung von Statoranlagen spezialisiert haben, setzen zunehmend auf moderne Materialien und erkennen deren Innovations- und Effizienzpotenzial. Durch die Integration dieser Materialien in den Fertigungsprozess können sie Statoranlagen herstellen, die nicht nur effizient sind, sondern auch den hohen Anforderungen der modernen Industrie gerecht werden.
Die Integration fortschrittlicher Materialien in die Statorfertigung hat das Feld revolutioniert. Diese Materialien, wie beispielsweise fortschrittliche Polymere, Verbundwerkstoffe und Hochleistungslaminate, bieten höhere Haltbarkeit, Hitzebeständigkeit und mechanische Festigkeit. Darüber hinaus steigert der Einsatz leichter, hochpermeabler Materialien den Gesamtwirkungsgrad deutlich. Dank der fortschreitenden Nanotechnologie können Hersteller nun Nanokomposite für Statorwicklungen entwickeln, die die Leistungsdichte weiter erhöhen und Verluste reduzieren. Dadurch werden Statoranlagen kompakter, effizienter und kostengünstiger, was Herstellern und der Industrie zahlreiche Vorteile bietet. Durch den Einsatz dieser fortschrittlichen Materialien sind Unternehmen der Statorfertigungsbranche für weiteres Wachstum und Innovation gerüstet.
3. Virtuelles Design und Prototyping: Ein Wendepunkt für die Entwicklung von Statorausrüstung
Virtuelle Design- und Prototyping-Technologie hat den Produktentwicklungsprozess für Statoranlagen revolutioniert. Früher mussten Hersteller ihre Designs ausschließlich auf physische Prototypen testen, was zeitaufwändig und teuer war. Dank virtueller Simulation und digitalem Prototyping können Hersteller nun Designs optimieren, potenzielle Mängel erkennen und die Produktleistung verbessern, bevor das Gerät tatsächlich produziert wird.
Mithilfe virtueller Design- und Prototyping-Software können Hersteller digitale Nachbildungen von Statoranlagen mit detaillierten Spezifikationen und Komponenten erstellen. Dieses digitale Modell kann bearbeitet und analysiert werden, um potenzielle Probleme oder Verbesserungspotenziale zu identifizieren. Durch virtuelle Simulationen können Hersteller die Leistung und Zuverlässigkeit von Statoranlagen unter verschiedenen Betriebsbedingungen testen und so fundierte Designentscheidungen treffen.
Einer der Hauptvorteile von virtuellem Design und Prototyping ist die Möglichkeit, potenzielle Defekte frühzeitig im Entwicklungsprozess zu erkennen. Durch die Simulation der Leistung der Statorausrüstung können Hersteller Schwachstellen oder Belastungspunkte identifizieren, die zu Ausfällen oder Defekten führen können. Dies ermöglicht ihnen, Designänderungen vorzunehmen oder alternative Materialien auszuwählen, um die Gesamtqualität und Haltbarkeit des Produkts zu verbessern.
Darüber hinaus ermöglicht virtuelles Design und Prototyping Herstellern, ihre Designs zu optimieren und so Leistung und Effizienz zu verbessern. Durch die Simulation von Geräten in einer virtuellen Umgebung können Hersteller verschiedene Designoptionen schnell bewerten und die optimale Konfiguration ermitteln. Dies reduziert die Anzahl der benötigten physischen Prototypen und spart im Entwicklungsprozess erheblich Zeit und Kosten.
Neben der Designoptimierung können auch virtuelles Design und Prototyping zur Verbesserung der Produktleistung beitragen. Durch die Simulation des Verhaltens von Statoranlagen unter verschiedenen Betriebsbedingungen können Hersteller potenzielle Leistungsengpässe identifizieren und notwendige Anpassungen zur Verbesserung der Produkteffizienz und -funktionalität vornehmen. Dadurch wird sichergestellt, dass das Endprodukt die geforderten Leistungsanforderungen erfüllt oder übertrifft.
Darüber hinaus ermöglichen virtuelle Design- und Prototyping-Technologien Herstellern, ihre Designabsichten Stakeholdern wie Kunden, Lieferanten und Aufsichtsbehörden effektiv zu kommunizieren. Detaillierte digitale Modelle ermöglichen eine klare Visualisierung und veranschaulichen die Funktionsweise des Stators in einem realen Szenario. Dies trägt dazu bei, die Zustimmung der Stakeholder zu gewinnen und sicherzustellen, dass das Endprodukt ihren Erwartungen entspricht.
Virtuelles Design und Prototyping bringen erhebliche Fortschritte im Produktentwicklungsprozess von Statoranlagen. Die Möglichkeit, Designs zu optimieren, potenzielle Defekte zu erkennen und die Produktleistung vor der eigentlichen Produktion zu verbessern, spart Herstellern Zeit und Kosten. Virtuelle Design- und Prototyping-Technologie ist zu einem unverzichtbaren Werkzeug in der Branche geworden und ermöglicht es Herstellern, hochwertige Statoranlagen zu entwickeln, die die Erwartungen der Kunden erfüllen oder übertreffen.
4.Maximierung der Effizienz: Wie sich Sensortechnologie auf die Statorherstellung auswirkt
Sensortechnologie bei der Herstellung von Statorgeräten Die Sensortechnologie spielt bei der Herstellung von Statorgeräten eine Schlüsselrolle, da sie Echtzeitüberwachung, Fehlererkennung und vorausschauende Wartung ermöglicht.
Durch den Einbau von Sensoren in die Statorwicklungen und andere Komponenten können Hersteller kritische Parameter wie Temperatur, Vibration und Isolationszustand kontinuierlich überwachen. Diese Sensoren liefern wertvolle Einblicke in den Zustand und die Leistung des Stators, ermöglichen eine proaktive Wartung und reduzieren ungeplante Ausfälle.
In der Welt derHerstellung von StatorausrüstungDie Aufrechterhaltung optimaler Leistung und die Vermeidung unerwarteter Ausfälle sind entscheidend. Statoren sind kritische Komponenten in verschiedenen Branchen, darunter Energieerzeugung, Industriemaschinen und Transportsysteme. Diese Maschinen arbeiten oft in rauen Umgebungen und sind hohen Temperaturen, Vibrationen und elektrischen Belastungen ausgesetzt. Statorausfälle können zu kostspieligen Ausfallzeiten, Produktionsausfällen und Sicherheitsrisiken führen.
Herkömmliche Wartungsmethoden basieren auf regelmäßigen Inspektionen und reaktiven Reparaturen. Dieser Ansatz ist jedoch oft ineffizient und ineffektiv. Er liefert keine Echtzeitinformationen über den Zustand des Stators, wodurch es schwierig ist, potenzielle Probleme zu erkennen, bevor sie eskalieren. Hier kommt die Sensortechnologie ins Spiel.
Durch die Integration von Sensoren in den Stator und deren Anschluss an Systeme zur Datenerfassung und -analyse erhalten Hersteller ein vollständiges Bild vom Zustand des Stators. Temperatursensoren können beispielsweise Hotspots überwachen und abnormale Temperaturanstiege erkennen, die auf eine mögliche Verschlechterung der Isolierung oder einen Ausfall des Kühlsystems hinweisen. Vibrationssensoren erkennen übermäßige Vibrationen, die auf Fehlausrichtung, Lagerverschleiß oder strukturelle Probleme hinweisen können. Isolationszustandssensoren überwachen den Zustand der Isolierung und warnen Hersteller vor möglichen Ausfällen oder Störungen.
Dank Echtzeitüberwachung können Hersteller frühzeitige Warnsignale für potenzielle Probleme erkennen und so rechtzeitig Wartungsmaßnahmen einleiten. Durch die schnelle Problembehebung können Hersteller unerwartete Ausfälle verhindern, Ausfallzeiten reduzieren und die Gesamtlebensdauer ihrer Statoranlagen verlängern. Darüber hinaus können die von Sensoren erfassten Daten zur Optimierung von Wartungsplänen genutzt werden, um eine effiziente und effektive Ressourcenverteilung zu gewährleisten.
Darüber hinaus ermöglicht Sensortechnologie eine vorausschauende Wartung, die potenzielle Ausfälle vorhersieht und proaktiv Maßnahmen zu deren Vermeidung ergreift. Durch die Analyse der von Sensoren erfassten Daten können Hersteller Muster und Trends erkennen, die auf potenzielle zukünftige Probleme hinweisen. Mit diesem Wissen können Hersteller vorausschauend planen, notwendige Ersatzteile bestellen und Wartungsmaßnahmen während geplanter Ausfallzeiten einplanen.
Sensortechnologie hat die Herstellung von Statoranlagen revolutioniert, indem sie Echtzeitüberwachung, Fehlererkennung und vorausschauende Wartung ermöglicht. Durch die kontinuierliche Überwachung wichtiger Parameter wie Temperatur, Vibration und Isolationszustand liefern im Stator integrierte Sensoren wertvolle Einblicke in dessen Zustand und Leistung. Dies ermöglicht Herstellern proaktive Wartungsmaßnahmen, reduziert ungeplante Ausfälle und optimiert die Gesamtleistung der Anlage. Dank Sensortechnologie ist die Herstellung von Statoranlagen in ein neues Zeitalter der Effizienz, Produktivität und Zuverlässigkeit eingetreten.
Abschluss
Technologische Fortschritte in der Statorfertigung verändern die Branche. Automatisierung und Robotik steigern Präzision und Effizienz, während moderne Materialien Haltbarkeit und Leistung verbessern. Virtuelles Design und Prototyping haben den Produktentwicklungsprozess revolutioniert, während Sensortechnologie Echtzeitüberwachung und vorausschauende Wartung ermöglicht. Die Umsetzung dieser Fortschritte verbessert nicht nur die Qualität und Zuverlässigkeit von Statoranlagen, sondern ermöglicht es Herstellern auch, den sich wandelnden Anforderungen verschiedener Branchen gerecht zu werden. Durch kontinuierliche Forschung und Entwicklung verfügt die Statorfertigung über ein größeres Innovationspotenzial und treibt so den Fortschritt in den Bereichen erneuerbare Energien, Transport und anderen Bereichen voran.
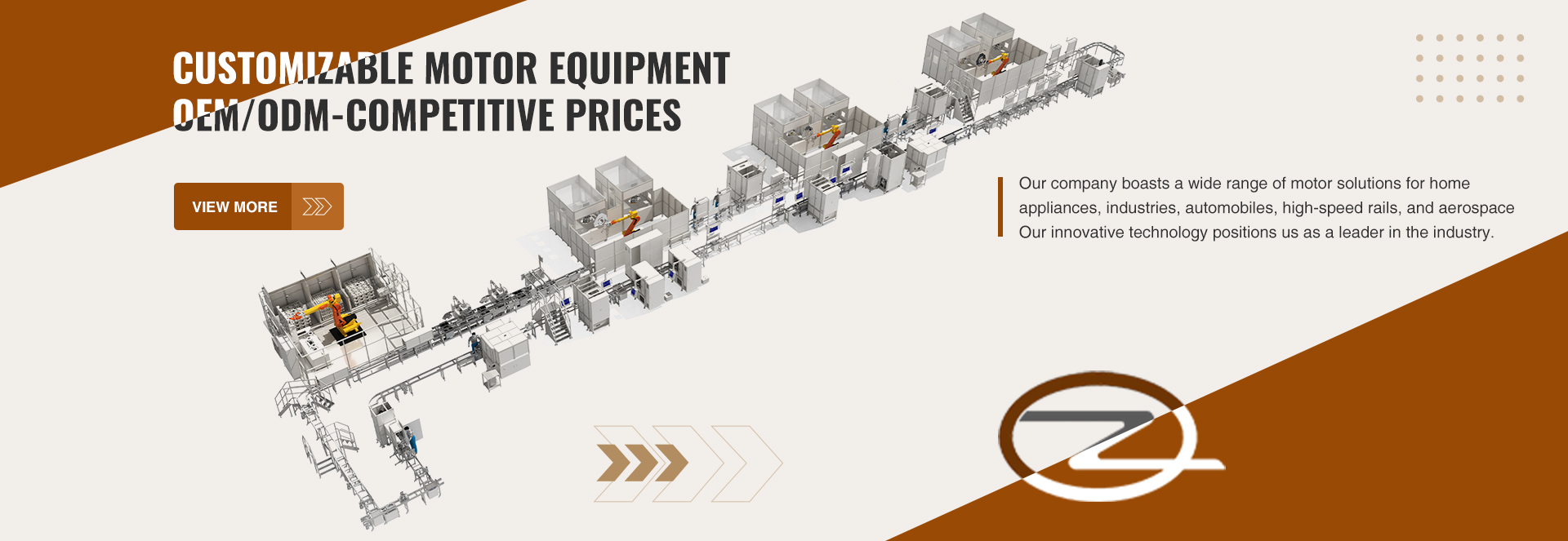
Guangdong Zongqi Automation Co., Ltd.produziert hauptsächlich Motorenfertigungsanlagen und integriert dabei Forschung und Entwicklung, Fertigung, Vertrieb und Kundendienst. Die Mitarbeiter von Zongqi sind seit vielen Jahren intensiv in der Fertigungstechnologie für die Motorautomatisierung tätig und verfügen über ein tiefes Verständnis der Fertigungstechnologie für motorbezogene Anwendungen sowie über umfassende Fachkenntnisse.
Unser UnternehmenProdukteDie Produktionslinien werden in den Bereichen Haushaltsgeräte, Industrie, Automobil, Hochgeschwindigkeitszüge, Luft- und Raumfahrt usw. eingesetzt. Die Kerntechnologie ist führend. Wir verpflichten uns, unseren Kunden umfassende automatisierte Lösungen für Wechselstrom-Induktionsmotoren und Gleichstrommotoren anzubieten.'s Herstellung.
Fühlen Sie sich frei,Kontakt us jederzeit! Wir helfen Ihnen gerne weiter und freuen uns auf Ihre Nachricht.
Adresse : Raum 102, Block 10, Tianfulai International Industrial City Phase II, Ronggui Straße, Bezirk Shunde, Stadt Foshan, Provinz Guangdong
Whatsapp/ Telefon:8613580346954
E-Mail:zongqiauto@163.com
Veröffentlichungszeit: 19. Oktober 2023